Ball Mill Cataracting Medium
.jpg)
Cascading (a) and cataracting (b) regimes in a tumbling mill
This study attempts to find optimal conditions of the friction coefficient using a discrete element method (DEM) simulation with various friction coefficient conditions and three different grindingOne of the most used tumbling mills is the ball mill This paper reviews different (PDF) Grinding Media in BAn experimental and numerical study on the grinding media dynamics inside a baffled ball mill under different solidflow regimes, namely, cascading, cataracting, and centrifuging, Experimental and Numerical Study of Grinding Media Flow in a Ball Mill 2023年4月23日 — One of the most used tumbling mills is the ball mill This paper reviews different types of grinding media that have been developed and improved over the years (PDF) Grinding Media in Ball MillsA Review ResearchGate
.jpg)
A Review of the Grinding Media in Ball Mills for Mineral
2023年10月27日 — The grinding media impart the forces required for size reduction and determine the category of tumbling mills: autogenous, rod mills and ball mills 2023年6月27日 — Cataracting regime holds a very important characteristic: the position of the shoulder and toe points The shoulder point is the highest angular position that the Experimental study of clinker grinding in a ball mill and 2017年8月29日 — There are two kinds of grinding body movements: either they describe an approximately parabolic trajectory, and knock against the material bed in a process TUMBLING MILL MECHANICS Springer2024年1月26日 — Axial rotation of ball mill provides cascading action of steel balls which crush the raw material due to attrition between steel balls which is known as grinding Computation of charging media for a double compartment cement ball mill
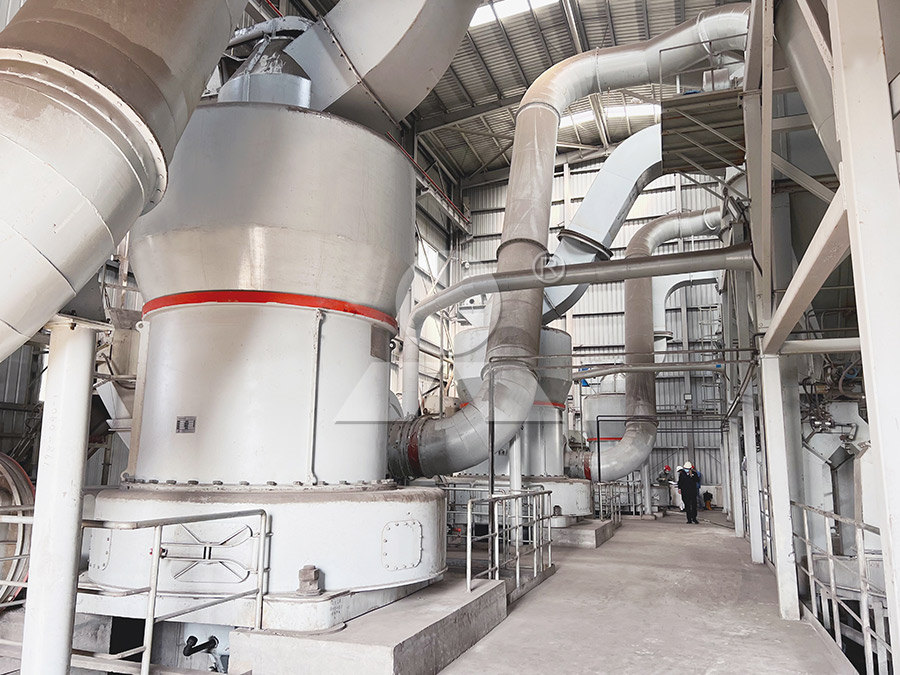
IOP Conference Series: Materials Science and
2020年5月4日 — Mill speed and lifter are the prime importance in the efficiency of comminution in ball mills, which seriously affect the charge motion Characterization on 2021年8月1日 — A dimensional analysis of the ball mill process is carried out through the BuckinghamPi method The dimensionless quantities identified are discussed and used Investigating grinding mechanisms and scaling criteria in a ball mill This contribution presents such a theory of the cataracting motion of grinding bodies in a planetary ball mill An analytical method for the evaluation of trajectories is given which Trajectories and impact velocities of grinding bodies in planetary ball 2016年11月7日 — The motion of the charge, that is the grinding media and the material undergoing grinding, within a mill is of considerable theoretical interest and practical importance, and for these reasons, has been the Grinding Media Charge Motion inside Mill
.jpg)
3: Mode of operation of a ball mill Download Scientific
The required speed of the ball mill with grinding media with innovative lifters at cataract mode of operation for the three types of materials is almost the same with an average value of 45% of CS2023年6月27日 — Experimental study of clinker grinding in a ball mill and the behavior of the grinding media inside the equipment using DEM this paper, the method was used to study the collisions between grinding media and grinding media and walls in ball mills, or cataracting, which favors the breakage by impact These two regimes have in commonExperimental study of clinker grinding in a ball mill and 2024年6月1日 — Ball mills are widely used for size reduction in mineral processing, but effective scaling from laboratory to industrial scale remains challenging This study introduces a novel scaling constant approach to replicate energy transfer to ore during milling across different scales by adjusting rotational speed and grinding medium size Scaling Energy Transfer in Ball Mills: A ScaleAgnostic 2022年6月1日 — ball media), and b is the coefficient which is equal to 0015 when ε is expressed in degree According to the equations of the critical rotational speed and rotation rate of the media in the mill, when the diameter of the grinding ball media in the mill is D=25 mm, the critical rotational speed can be calculated via the equation nc = 948 r OLQGULFDOEDOOPLOOLQFDVFDGLQJPRWLRQVWDWH
.jpg)
Trajectories and impact velocities of grinding bodies in planetary ball
The motion of grinding bodies in conventional ball mills has been repeatedly investigated, both theoretically and experimentally It is well‐known that, depending on mill filling and speed of rotation, different motion patterns occur and some of these patterns, especially that of cataracting, can be described by simplified theories2015年11月11日 — MILL INTERNALS OCTOBER 2015 ICR XX Ball mills require frequent attention in terms of their wear parts The appropriate selection of mill internals not only protects the mill shell, saving on costly repairs, but in some cases, improves mill performance Figure 2: movement of the balls in the mill Cataracting medium Empty zone ICR article draft thecementgrindingoffice1992年9月1日 — It can be an important com ponent of any control system with variable mill speeds, feed rates, etc Fi nally, it could conceivably be employed to estimate the power requirements of tumbling mills other than ball mills, such as rod mills, autogeneous mills, etc ACKNOWLEDGEMENTS The authors express appreciation to the United States Bureau A cascadecataract charge flow model for power draft of tumbling mills There are three types of grinding media that are commonly used in ball mills: • steel and other metal balls; • metal cylindrical bodies called cylpebs; • ceramic balls with regular or high density Steel and other metal balls are the most frequently used grinding media with sizes of the balls ranging from 10 to 150 mm in diameter [30]Grinding in Ball Mills: Modeling and Process Control
.jpg)
Estimation of shear rates inside a ball mill ScienceDirect
1999年9月1日 — Section snippets General approach Two types of ball motion were considered for the determination of shear rates: cascading and cataracting Cascading refers to the condition where the grinding media tend to roll down to the toe of the charge, whilst in cataracting the media are projected clear of the charge to describe a series of parabolas 2023年10月30日 — Ball mills are the foremost equipment used for grinding in the mineral processing sector Lifters are placed on the internal walls of the mill and are designed to lift the grinding media (balls Analyzing the influence of lifter design and ball 2017年7月1日 — A coupled slurrymedia model of mill discharge and trommel flow is developed Streams of cataracting balls thrown by the discharge head lifter bars are not directed towards the discharge opening and therefore do not tend to enter the trunnion The crosssectional profile of the end wall lifter geometry considered here has inclined sides Combined DEM and SPH simulation of overflow ball mill 2017年7月1日 — In order to observe these transitions, experiments were carried out in a tumbling mill of 300 mm diameter, and three sizes of chrome steel balls were used as grinding media Each size of ball was Experimental Study of Charge Motion in a Tumbling Ball Mill
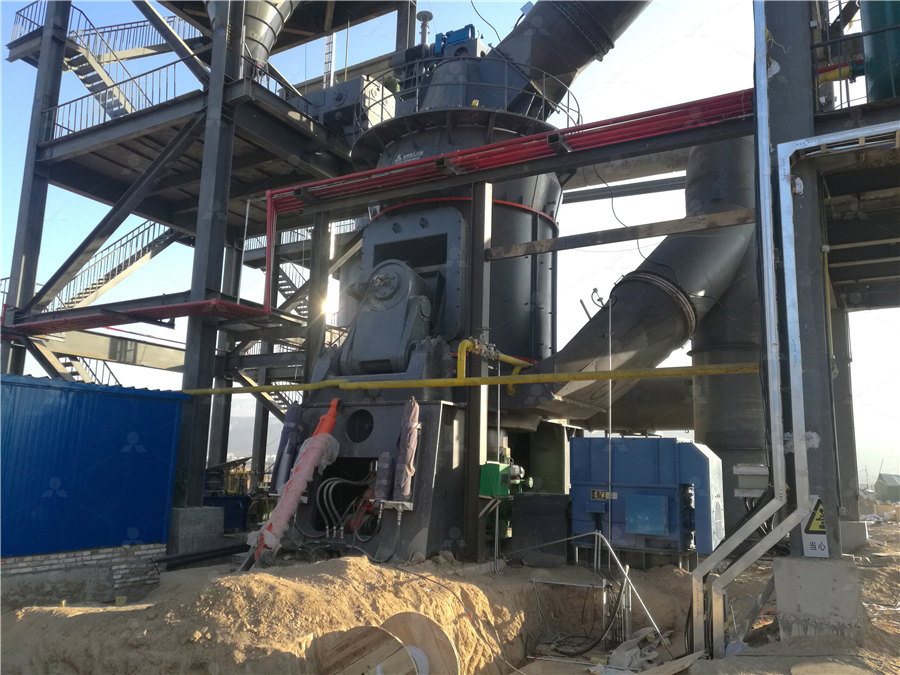
Examples of movement of the media inside a ball mill
Download scientific diagram Examples of movement of the media inside a ball mill simulated using DEM: centrifuge (left), cataract (middle) and cascade (right) from publication: Effect of 1999年9月1日 — This study was aimed at the derivation of an estimate of a typical shear rate range inside a ball mill, in order to determine appropriate values of apparent viscosity for studies of the effects of rheology on grinding whilst in cataracting the media are projected clear of the charge to describe a series of parabolas before landing on or Estimation of shear rates inside a ball mill ScienceDirect2019年10月12日 — Industrial tumbling mills typically operate in the high Froude range (cascading or cataracting) and exhibit a rich coexistence of flow regimes (Mellmann, 2001) that are bounded by nonlinear surfaces as illustrated in Fig 1 1 The “rising enmasse” region is dense and follows closely the rotation of the drumFlowing atop the rising en Geometric features of tumbling mill flows: A positron 2017年7月1日 — When the mill charge contained monosized balls, the ball flow regime inside the mill transited to the cataracting and impact breakage was the main breakage mechanismThe effect of ball size distribution on power draw, charge
.jpg)
Investigating grinding mechanisms and scaling criteria in a ball mill
2021年8月1日 — Ball mills are one of the most common industrial equipments for reducing the size of particulate systems in various fields such as cement industry, minerals or nuclear fuel production [1]In such equipment, the powder is ground due to the movement of the grinding media, also called pebbles, within a rotating vesselHow Ball Mills Lifter Bar Affects Charge MotionHow Ball Mills Lifter Bar Affects Charge Motion2013年2月7日 — Scheme of a ball motion pattern in a single pot of a planetary ball mill – (a) cascading, (b) cataracting, (c) rolling nfluence of varied frictional coefficients on simulated ball motion (PDF) Process Engineering with Planetary Ball 2022年8月18日 — Discrete Element Methods (DEM) is a numerical tool consolidated to the simulations of collisions in particulate systems In this paper, the method was used to study the collisions between grinding media and grinding media and walls in ball mills, which is the most used unit operation in clinker grinding, the majority component of the cement Experimental study of clinker grinding in a ball mill and the
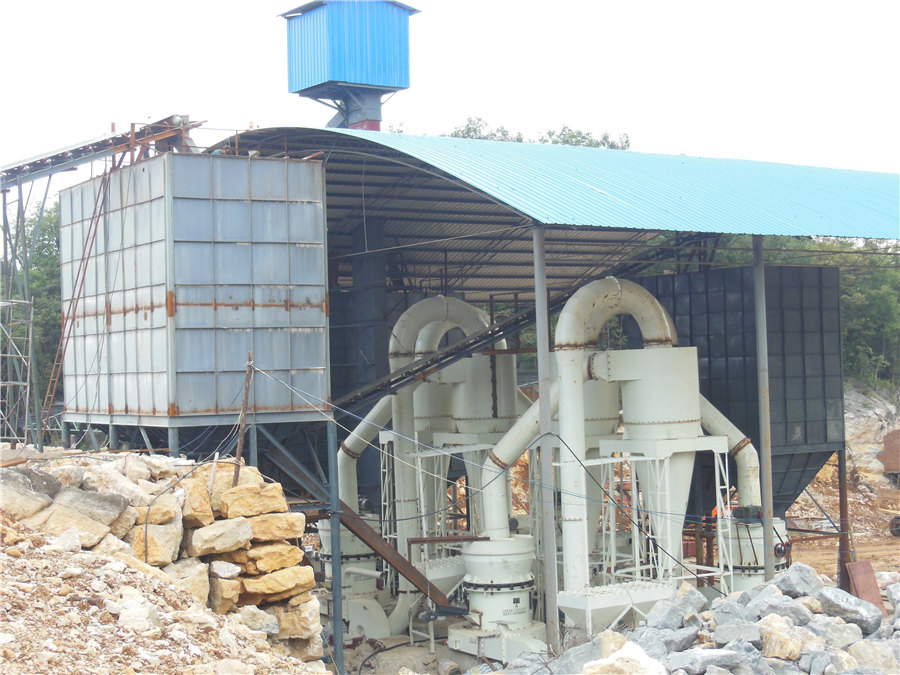
cataracting in the ball mill kooksco
cataracting action in ball mills rodekruisnijmegengala cataracting action in ball mills 34238 paverco Predicting charge motion, power draw, segregation and wear, cataracting action in ball mills 34238,Much of the core of the charge is now cataracting Mills are generally run subcritical (N ) because little grinding can be acMeved with the 2024年6月1日 — The energy efficiency of ball mills is typically low, with only 1–5% of the input energy used for particle breakage while the rest is lost as heat [18] The power draw of a ball mill is determined by the charge motion inside the mill, which is influenced by factors such as mill speed, ball filling, and lifter design [19–21]Scaling Energy Transfer in Ball Mills: A ScaleAgnostic 2017年7月1日 — Tumbling ball mills are a common comminution device in the mineral industry processing, wherein the particle size reduction is performed by action of the grinding media Different forms of transverse motion in a rotating cylinder have been studied by many researchers The aim of this paper was to study the transitional phenomena between Experimental Study of Charge Motion in a Tumbling Ball Mill2024年1月26日 — Grinding media is mostly prepared from high chrome steel Ball mills are efficiently utilized for final grinding of clinker It grounds the raw mix (clinker) into fine powder Ball mills are available of different sizes and capacities Ball mill may be of two compartment or three compartments The schematic view of cement ball mill is shown in Computation of charging media for a double compartment cement ball mill
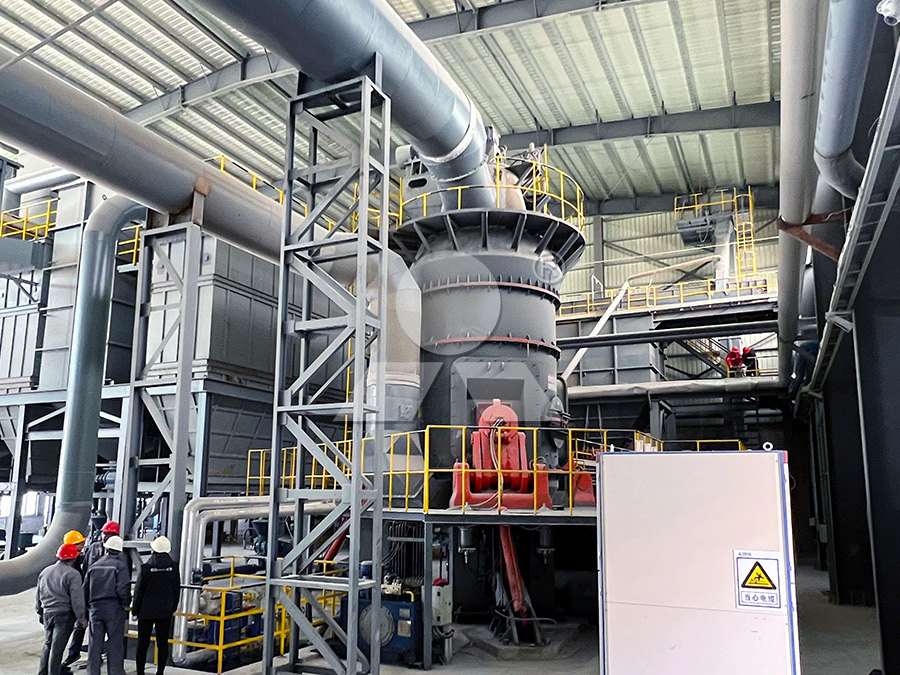
Crosssection of typical ball mills showing various
The ball mill is a rotating cylindrical vessel with grinding media inside, which is responsible for breaking the ore particles Grinding media play an important role in the comminution of mineral Cataracting Cataracting terjadi ketika putaran mill relatif tinggi, tetapi tidak mencapai kecepatan kritis Muatan berputar dan bergerak naik relatif tinggi hingga mencapai titik kesetimbangan Saat muatan bergerak mencapai titik kesetimbangan, muatan akan jatuh bebas ke dasar mill (impact zone)Grinding on mineral processing Abstrak – Praktikum Modul Although there are instances in which ball mills have been successfully operated at speeds ranging from 60% to 90% of their critical speed, it is a common practice to run the mills at speeds Cascading (a) and cataracting (b) movement in a rotary cylinder 2013年12月30日 — speed continuing to increase, cataracting movement is more obvious, and drop points of steel balls moved up and the impact velocity of steel balls is also faster Keywords: Ball Mill; Discrete Element Method; Movement of Single Diameter of Steel BallsThe Simulation and Analysis on Medium Motion in Ball
.jpg)
Dissipation behavior of granular balls in a rotating closed
2023年7月14日 — The discrete element method is used to study the dissipation behavior of the granular balls in a rotating closed cylinder under the Earth gravity environment, and five kinds of particle motion forms with different dissipation characteristics are obtained These phases are slumping, rolling, cascading, cataracting and centrifuging Combined with the 2018年1月4日 — The drive of the ball mill consists of an induction electric motor, twostage gearbox and the pinion gear This pinion gear is mated with the girth gear mounted on circumference of the ball mill shell and in that way it transfers the motion from the drive to the shell, see Figure 1, taken from [1] Figure 1 Mechanical system of a ball mill AN EXPERIMENTAL ANALYSIS OF VIBRATION OF A BALL The shell liner type, rotation speed, and ball filling percent are the key factors influencing the charge behavior inside the SAG mills, and consequently, their performanceIndustrial SAG mill dimensions and speeds2020年5月14日 — Effect of Lifter Shapes on the Mill Power in a Ball Mill To cite this article: Zixin Yin et al 2018 IOP Conf Ser: Mater power increases to a maximum with increasing mill speed for all media shapes Kiangi et al [9] used an amount of cataracting charge impacts the mill shell and bulk toe, the charge shape in cascading region PAPER OPEN ACCESS Effect of Lifter Shapes on the Mill
.jpg)
(PDF) Grinding in Ball Mills: Modeling and Process Control
2012年6月1日 — There are three types of grinding media that are commonly used in ball mills: modes: slow rotation (cascading), fast rotation (cataracting) and very fast rotation Ball mills can grind a 2020年4月16日 — Bentuk gerigi dalam raw mill mempengaruhi efektivitas gerak steel ball Gerigi dalam raw mill didesain sedemikian rupa, hal ini bertujuan untuk mempermudah terjadinya mode gerak cataracting Dengan adanya gerigi ini, kecepatan rotasi yang dibutuhkan untukPengaruh Mode Cataracting dan Cascading dalam 1994年2月1日 — TABLE2 Data used in the ball mill experiment Mill diameter 254 cm Mill length 292 cm Mill speed 70% of critical Lifter bar height (8) 032 cm Number of balls 109 Total ball weight 305 kg Average ball weight 028 kg Limestone holdup 33 kg Energy consumed 78 J/revolution SIMULATION OF CHARGE MOTION IN BALL MILLSSimulation of charge motion in ball mills Part 1: 2017年6月12日 — This paper involves an experimental and numerical study on the grinding media dynamics inside a baffled ball mill under different solid flow regimes: cascading, cataracting and centrifugingExperimental and Numerical Study of Grinding Media Flow in a Ball Mill
.jpg)
Diameter factors affecting ball mill scaleup ScienceDirect
1988年4月1日 — Additional research work is needed on scalingup laboratory and pilotplant ball mill data to predict the performance of large diameter ball mills is derived in which the complex and varied patterns of tumbling charge movement are represented by coupled cascadingcataracting flows, with or without the superimposition of centrifuging and 2018年12月4日 — Snapshots showing the motion of particles on the pilot scale ball mill with no lifter (a) using DEM simulation method (single solid phase); (b) using DEMSPH coupling method (two phase)(PDF) Combined DEM and SPH simulation of ball milling2016年11月7日 — The motion of the charge, that is the grinding media and the material undergoing grinding, within a mill is of considerable theoretical interest and practical importance, and for these reasons, has been the Grinding Media Charge Motion inside MillThe required speed of the ball mill with grinding media with innovative lifters at cataract mode of operation for the three types of materials is almost the same with an average value of 45% of CS3: Mode of operation of a ball mill Download Scientific
.jpg)
Experimental study of clinker grinding in a ball mill and
2023年6月27日 — Experimental study of clinker grinding in a ball mill and the behavior of the grinding media inside the equipment using DEM this paper, the method was used to study the collisions between grinding media and grinding media and walls in ball mills, or cataracting, which favors the breakage by impact These two regimes have in common2024年6月1日 — Ball mills are widely used for size reduction in mineral processing, but effective scaling from laboratory to industrial scale remains challenging This study introduces a novel scaling constant approach to replicate energy transfer to ore during milling across different scales by adjusting rotational speed and grinding medium size Scaling Energy Transfer in Ball Mills: A ScaleAgnostic 2022年6月1日 — ball media), and b is the coefficient which is equal to 0015 when ε is expressed in degree According to the equations of the critical rotational speed and rotation rate of the media in the mill, when the diameter of the grinding ball media in the mill is D=25 mm, the critical rotational speed can be calculated via the equation nc = 948 r OLQGULFDOEDOOPLOOLQFDVFDGLQJPRWLRQVWDWH The motion of grinding bodies in conventional ball mills has been repeatedly investigated, both theoretically and experimentally It is well‐known that, depending on mill filling and speed of rotation, different motion patterns occur and some of these patterns, especially that of cataracting, can be described by simplified theoriesTrajectories and impact velocities of grinding bodies in planetary ball
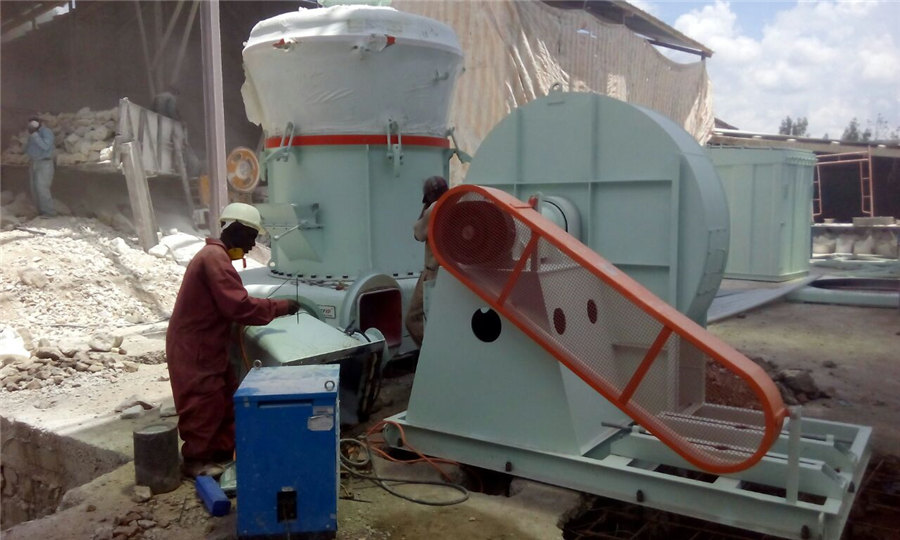
ICR article draft thecementgrindingoffice
2015年11月11日 — MILL INTERNALS OCTOBER 2015 ICR XX Ball mills require frequent attention in terms of their wear parts The appropriate selection of mill internals not only protects the mill shell, saving on costly repairs, but in some cases, improves mill performance Figure 2: movement of the balls in the mill Cataracting medium Empty zone 1992年9月1日 — It can be an important com ponent of any control system with variable mill speeds, feed rates, etc Fi nally, it could conceivably be employed to estimate the power requirements of tumbling mills other than ball mills, such as rod mills, autogeneous mills, etc ACKNOWLEDGEMENTS The authors express appreciation to the United States Bureau A cascadecataract charge flow model for power draft of tumbling mills There are three types of grinding media that are commonly used in ball mills: • steel and other metal balls; • metal cylindrical bodies called cylpebs; • ceramic balls with regular or high density Steel and other metal balls are the most frequently used grinding media with sizes of the balls ranging from 10 to 150 mm in diameter [30]Grinding in Ball Mills: Modeling and Process Control